Get a quote, configure a custom safety solution or ask a question. We're here to help!




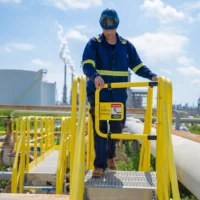



- Spill ContainmentMore …Loading Safety CagesMore …
SafeRack Worldwide
We pride ourselves on one-on-one customer service. When you call SafeRack, we'll be there to answer your questions with a combined experience of 400+ years.
Select your region below.- View Products
- Railcar & Truck Loading Platforms
- Gangways & Loading Ramps
- Stairs, Platforms & Ladders
- Mobile Ladders & Platforms
- Loading Arms & Fluid Transfer
- Safety Gates & Traffic Control
- Aviation & Aerospace Access
- Marine Access & Loading
- Grounding & Monitoring
- Spill Containment
- Loading Safety Cages
- Transloaders & Skids
- Shelters & Canopies
- Fall Protection
- Terminal & Speciality
Home / Industries / Power PlantsPower Plants
SafeRack has successfully installed safety solutions in power plants throughout North America. But we do more than install those innovative systems, we support them with the industry’s best customer service. While the energy produced by the nation’s power industry is vital to our way of life, power generation plants pose an array of workplace dangers.
Keeping your workers safe is a constant challenge, as a mistake at your plant can easily prove fatal. Thankfully, the risks associated with power generation can be greatly reduced through safe work practices.
Question, Get a Quote, Live Demo or Request an On-Site Visit
Our experts simplify the complex
View Full TextGenerator Access and Maintenance
Generators can give years of reliable service, but that’s typically only possible with regular maintenance.
Performing regular maintenance will ensure your industrial generator will operate reliably, helping your business avoid the financial losses associated with a shutdown.
ErectaStep’s generator access and maintenance platforms and stairs are prefabricated, modular, solid, safe, and OSHA certified! ErectaStep access solution makes generator maintenance safe and simple at your data center, pipeline terminal, or distribution center.
10 Minute Tips: Power Plant Safety Reminders
Here are the four main areas of concern regarding power plant safety:
Arc Flash Avoidance
While electrocution is often cited as the biggest hazard facing power plant employees, the vast majority of electrical injuries at power plants are actually the result of arc flashes.
The massive electrical currents created in power plants make arc flashes extremely dangerous. When a flashover of a current at a plant veers off its intended path and travels through the air from one conductor to another or a ground, anyone in close proximity is at risk for serious injury, like burns, or even death. Those who survive arc flashes often struggle to regain their prior quality of life and can require extensive and costly medical care.
Arc flashes can be caused by numerous things, including:
- Dust
- Dropped tools
- Accidental contact/touching
- Condensation
- Material failure
- Corrosion
- Faulty installation
In order to reduce arc flashes, your plant should focus on the above hazards, as well as decrease fault clearing times, reduce fault currents, and increase the distances between arcs and workers.
You can further protect your employees from flames and electric arcs by mandating that all employees wear heat-resistant PPE with an arc rating greater than or equal to the maximum available heat energy, and that will not melt or ignite when exposed to the maximum potential heat energy a particular hazard can produce.
Your plant should also indicate arc flash hazards by utilizing highly visible arc flash labels, along with floor markings to mark safe approach distances.
Fall Prevention
DCO Energy was dismayed that the manufacturer of their boiler had no access solutions around their equipment. We offered access catwalks and rolling ladders to solve their maintenance issues and for DCO to pass the state-mandated annual inspections and ensure worker safety against electrical hazards around the boiler plant. Falls from elevations remain a leading cause of occupational injuries and fatalities, and that includes falls at power plants.
Fall hazards affect employees both on the ground and working up high. Tasks like welding, installation, and maintenance are almost always performed overhead. Workers regularly climb up and down ladders and work on scaffolding significantly higher than four feet in the air. Falls can occur as a result of unsafe platforms, slipping and tripping, contact with electrical energy, human error, and more. As a result, it is crucial that your plant has a comprehensive fall protection strategy, as well as regular fall protection training and education for employees.
That training should include:
- Educating your employees on recognizing fall hazards and how to handle them
- Encouraging and educating reporting of near-miss incidents to ensure fall protection equipment is used to prevent future near-misses
- Discussing which fall protection PPE items work best, as well as what new items could be incorporated
- Conducting employee training on safety policy and requirements, including dispelling reasons for non-compliance
- Implementing task-specific safety briefings prior to the start of each project
In addition to providing proper safety training, your plant should also provide the appropriate tools and equipment to protect your employees from falls.
Per OSHA guidelines, workers cannot be allowed to fall more than 2 feet before their safety equipment kicks in. They shouldn’t be able to fall and come into contact with a lower level, and they must be tethered securely if they are more than 4 feet off the ground.
Not only must the fall protection used by employees be flame resistant, but it must also be able to withstand a high amount of force during a drop test (starting at 4,000 pounds).
Floor tape can help provide extra traction, while labels and signage can help to identify the location of fall-prevention equipment, secure tie-off points, and known environmental hazards.
Loading platforms can help your workers move more efficiently, seamlessly, and safely. Crossover platforms provide safe passage over areas with obstructions, danger zones, and other hazards. Swing gates can help your facility comply with OSHA regulations by covering multiple openings, and helping to keep your team productive and safe.
Confined-Space Hazard Mitigation
Confined spaces can pose serious safety hazards at power plants.
Workers regularly enter confined spaces when performing maintenance, unaware that simply poking their heads through an opening can expose them to oxygen-deficient or toxic atmospheres. All too often, employees fail to test and evaluate atmospheres prior to entry, nor conduct any monitoring while working. When dangerous incidents happen, rescues are usually spontaneous, unplanned reactions that can also put rescuers at risk. In fact, roughly 60% of fatalities in confined-space incidents involve employees trying to rescue their colleagues.
You can minimize fatalities and lower your plant’s injury rate by properly identifying confined spaces with signs and providing tools to help employees perform their work without needing to enter dangerous spaces.
Employees should follow OSHA requirements for restricted exit and entry regarding confined spaces. Warnings must be prominently displayed in all hazard zones, and barricades are recommended for preventing unauthorized access. Employees accessing confined spaces must wear personal protective equipment (PPE) and ambient air and personal monitoring to ensure their safety.
Fire and Explosion Prevention
While arc flashes might account for the biggest number of electrical injuries at power plants, explosions and fires have been responsible for some of the worst accidents at various types of power generation facilities over the past 100 years.
Some of the most common causes of fires and explosions — at power plants and in other industrial settings — include:
- Combustible dust
- Welding, torch cutting, brazing, burning, heating, soldering, and other “hot work”
- Flammable liquids and gasses
- Faulty equipment and machinery
- Inadequate, incomplete, and/or delayed maintenance
- Electrical hazards
The key to preventing fires and explosions is establishing comprehensive safety policies and procedures, and then implementing them throughout your plant.
Follow these steps:
- Conduct a hazard analysis of your facility to identify problem areas and risks so you can address them. Repeat the process on a regular basis, including when you make any changes to your facility or install any new equipment.
- Make sure your fire prevention and emergency procedures cover everything from employee smoking to PPE to an emergency evacuation plan. Ensure all team members can view or access these documents at all times.
- Provide general and job-specific fire safety training for all employees working in potentially hazardous atmospheres and conditions.
- Implement a regular housekeeping routine to reduce the chances of sparks or static discharge causing an incident.
- Inspect and maintain all equipment and systems, including inspecting and testing your fire safety systems and gear every six months.
Mobile work platforms can provide safe and cost-effective access for maintenance and inspection of hard-to-reach boilers and other structures.
Is your plant or facility compliant with ANSI, OSHA, and local safety codes? We can help!
EMERGENCY EYEWASHES / SHOWER EQUIPMENT AND THE ANSI/ISEA Z358.1 – 2014 STANDARD
Following eye contact, you must start washing with water immediately to prevent permanent damage. In the event of skin contact, you must start washing with water immediately to prevent slow-healing chemical burns.
Are you aware that ANSI guidelines state that Eye Wash/Drench Showers need to be located 10 seconds or 55′ from contaminates or hazardous materials and located on the same horizontal plane, with no obstructions? If bottom loading/unloading, an additional shower should be located at grade as well. SafeRack provides the above equipment plus much more needed to keep employees safe and expedite bulk chemical loading and unloading.
OSHA Regulation Experts – Does your existing chemical safety equipment or chemical loading systems meet OSHA’s latest requirements? SafeRack’s professional technical sales consultants are available to meet with your team to make recommendations to keep your facility in front of OSHA’s ever-changing country and region-specific standards and regulations, including lifeline and trolley beam fall arrest systems, metal stairs, and access platforms.


Quick Quote 866-761-7225
LET US DESIGN YOUR SOLUTION TODAY
Our innovative tools provide 3D visualizations and accurate quotes in minutes.
Get Help NowOrder Now 866-761-7225
Questions or Need a Quote?
Chat live with a knowledgeable and friendly safety expert now.

Bob Kashtan
Located in South Carolina

Joey Robinson
Located in South Carolina

Caelin Lacy
Located in South Carolina

Katie Kelly
Located in South Carolina

Amber Graham
Located in South Carolina