Get a quote, configure a custom safety solution or ask a question. We're here to help!




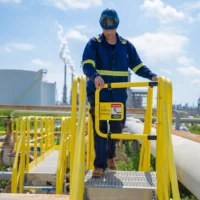



- Spill ContainmentMore …Loading Safety CagesMore …
SafeRack Worldwide
We pride ourselves on one-on-one customer service. When you call SafeRack, we'll be there to answer your questions with a combined experience of 400+ years.
Select your region below.- View Products
- Railcar & Truck Loading Platforms
- Gangways & Loading Ramps
- Stairs, Platforms & Ladders
- Mobile Ladders & Platforms
- Loading Arms & Fluid Transfer
- Safety Gates & Traffic Control
- Aviation & Aerospace Access
- Marine Access & Loading
- Grounding & Monitoring
- Spill Containment
- Loading Safety Cages
- Transloaders & Skids
- Shelters & Canopies
- Fall Protection
- Terminal & Speciality
Home / Industries / Cement, Fly Ash & Frac Sand Loading / Dry Bulk LoadingDry Bulk Loading
Dry Bulk Loading Solutions
The cement industry has the most truck loadouts per day of any industry. Getting dry bulk trailers loaded/unloaded and in and out in a safe, efficient manner is key to the bottom line.
Truck drivers have a choice as to what facility they go to for cement to load their dry bulk trailers. Not just the aging population, but also the less physically strong and those wanting easy to use equipment tend to gravitate toward facilities that cater to their needs, and that is why drivers want to go into plants and terminals that deploy SafeRack systems.
Cement & Frac Sand | Dry Bulk | Hopper Car | Silo Valve Access | Flatbed | Railcar
Question, Get a Quote, Live Demo or Request an On-Site Visit
Our experts simplify the complex
View Full TextYour Project
Quote or discuss your installation.
Start by selecting loading application"*" indicates required fields
Below are some of the loading and unloading solutions for illustrative purposes only. Our experts will work with you and your team for a custom solution to suit your needs.
Typically, as a starting point, we will need to know answers to these questions for your project- Do you require a new platform system or retrofitting to the existing platform?
- How many trucks per day cycle through your facility?
- What types of vehicles are being accessed?
- Is a manual system or powered system required?
- What are your expectations on lead times?
- Would you like a turn-key solution?
- Are you interested in reducing or eliminating lower back strains at your loading racks?
In addition, we undertake a detailed site survey to check and clarify all dimensions and other salient issues.
Top Hatch Access Platforms
Platform design is dictated by application or form of function. Many factors are considered when creating a solution. Available real estate at a facility, types of vehicles, traffic patterns, and desired throughput are all taken into consideration during the design phase. Retrofit applications are routine exercise for our staff. There is an existing population of thousands of loading racks in the cement industry with many varying designs. We can readily implement our years of experience to provide an industry best turn around on drawings and equipment delivery. In fact, most applications can be laid out on-site by our sales staff using proprietary, state of the art 3D software that can produce approval drawings and equipment pricing before leaving your facility.
Dry bulk trailer configurations can be single, multi-hatch, or pup style. Additionally, some facilities will service multiple types of vehicles, like loading proppant boxes along with dry bulk trucks.
Loading Gangways with Safety Cages
Standard widths on cement gangways is 24″. Wider style gangways are available when circumstances warrant. Powered gangway solutions are also an option, with both hydraulic and dry bulk solutions being commonly used. Each gangway will be fitted and factory balanced with a cement industry-specific extended profile cage. These were designed in collaboration with leading industry cement companies to address cement specific needs. Accommodating multiple hatch opening orientations while decreasing gaps between the access system and vehicle to prevent operators from falling off is the primary focus.
GX SELF-ADJUSTING STAIR (SAS) GANGWAY
SafeRack’s NEW GX SAS gangways uses Retractalok power-assist technology allowing operators to raise or lower effortlessly, light as a feather to lift, solid as a rock. Tested in the most critical applications, this revolutionary new gangway outperforms all others. Available in multiple lengths and widths. Learn More
Loading Chutes
In some instances when budgets or lack of real estate drive this requirement we can design and layout systems that work in conjunction with loading chutes in silos. Typically these applications are very limited spatially and require modifications to gangway storage positions and cage design and layout. Over the years SafeRack has developed design techniques that mitigate silo limitations. SafeLok Systems
Another system option that was developed jointly with cement producers. It prevents truck drivers from raising the gangway and cage systems which would create an unsafe condition where the operator could fall under the cage while negligently trying to lift it to open or close an improperly spotted truck hatch. Early Departure Systems
Interlock Systems
The device increases safety at your loading spot and helps prevent damage to your loading racks. A driver or operator attaches the interlock fitting to the braking system of the truck, guaranteeing the process you put in place will be followed before the tanker can be loaded.
Truck Traffic Gates
Traffic Gates on specially designed elevated pedestals are synchronized with gangway and cage operations. The traffic gate will lower when the gangway system is lowered creating a visual and physical barrier that reminds truckers to raise the system before driving off. An option for high visibility red and green LED illumination can be integrated into gates for an even higher level of drive-off protection.
Gangway Extended Top Handrail
The SafeRack handrail extension helps prevent truck drive-offs while the gangway is in a lowered position. The elongated safety orange top handrail extends into the platform to remind drivers to properly store equipment before leaving the platform and returning to their trucks.
Safety Orange Cages
Standard aluminum cages factory finish blend in with dry bulk truck colors. Our bright safety orange powder coat finish improves visibility and prevents early drive offs that damage the loading platform and equipment, creating downtime.
Magnetic Swing Gates
A magnetic safety gate can be linked to any gangway and cage operation. When the gangway and cage are in the down position a proximity switch engages the swing gate lock to prevent egress from the loading rack platform. Operators can freely leave the platform once the system is in proper stored position.
Safety Gates
Safety Gates will be installed at the top of stairs and any other openings to ensure operator safety at all times. YellowGate Safety Gates
SafeRack’s line of industrial safety gates is the most flexible product on the market with the ability span openings between 16” and 36” and is field adjustable with nothing more than a wrench. Learn More
Loading Options
- Lighting – Lighting both over and under the platform will be provided. For overcast days or second shift, lighting is essential for improved safety and improved productivity.
- Platform & Canopies – Full platform canopies reduce exposure to the elements and improve the safe and productive loading operation from the operator’s perspective.
- Operator Shelter – Depending on your site requirements, consideration should be given to the requirement of an operator or guard building on the loading platform. This can be customized to meet specific site requirements
- Wheel Chocks – Railcar Wheel Chocks provide fast blocking of all types of railcars and meet OSHA regulations to safely prevent railroad cars from moving during loading or unloading operations. This is a requirement by the Department of Homeland Security
TURN KEY OFFERING
We can provide installation services on our equipment. Using our certified installation group ensures a quick, professional installation done by qualified personnel who can guarantee the equipment is in proper working order when the job is complete. Operator training is a standard part of this service. * For illustrative purposes only. Our experts will work with you and your team for a custom solution to suit your needs Why choose SafeRack for dry bulk loading? There are many reasons why SafeRack cement access gangway systems have become the industry standard.
- Our designs and innovations precipitate from Customer requests and needs.
- We have engineered and patented designs that are specific to the dry bulk loading.
- Many of these designs are collaborations with top companies wanting to reduce or eliminate accidents involving antiquated access equipment.
- We have raised the bar on ergonomics, safety, and throughput.
Safer Dry Bulk Loading
SafeRack’s innovative offset safety cage features flared and tapered rungs that is specially designed for dry bulk trailers, giving the lid or manhole a full range of motion to open and close the hatches. The design also ensures that the gangway and cage will not interfere with hatch access and movement when the equipment is lowered on top of the truck.
Railroad Fuel Loading Gangway With A Safety Cage and a Spill Containment Pan Keeping cement truck drivers safe and happy when dry bulk loading is key to them wanting to choose a particular cement company for product .
They have a choice. Many times, the aging population and less physical or strong drivers gravitate toward easy to use equipment. Our systems fit the bill.
The cement industry has the most truck loadouts per day of any industry. Getting dry bulk trucks in and out in a safe efficient manner is key to the bottom line. Drivers gravitate to facilities that cater to their needs. That is why drivers want to go into plants and terminals that deploy SafeRack systems.
We have the best delivery of any access system company in the industry. We leverage our state of the art manufacturing equipment and techniques to provide deliveries measured in days not the industry accepted weeks. This allows for plants and terminals to keep their loadouts open and product flowing.
Our flexibility and willingness to provide the highest level of customer service has produced commercial stocking agreements with companies requiring 24-48 hour replacements.
Dry bulk loading process
Loading sand, clay, and many other materials into a dry bulk trailer is a relatively simple process. The driver pulls the truck under a chute attached to a silo, and gravity does most of the work as the material drops through the manhole. The process moves from one manhole to the next, to fill the trailer evenly
Loading plastic pellets or powder from a rail car is trickier, however, as it involves the use of air pressure to move product through the hose and into the trailer. It takes a skilled worker to pressurize the trailer in just the right way and then gently adjust the air to get the product moving.
Usually, the shipper assigns an employee to take charge of loading. But, before anyone starts that process, you need to inspect the trailer carefully to make sure it’s clean, dry, and odor-free. You can ask the carrier for a wash slip to confirm that the trailer has been cleaned correctly. Additionally, the seals on the manholes and the valves on the hoppers must be checked to make sure they’re closed tightly so that no product can leak out.
Dry bulk unloading process
Unloading is generally a driver’s job. Every piece of equipment is different, and the driver is the expert on how his equipment behaves.
When the driver arrives at a plant or other receiving site with a load, his first stop is the office. He shows his paperwork and confirms that the product on the truck is the same product the company expected. If the driver is offloading into a silo, he will then verify the correct silo with the receiving site personnel. A smart driver will get an authorized person to sign a form attesting to that fact, to make sure he’s held harmless in case of a mistake.
To begin the unloading, the driver brings the truck as close as possible to the silo. If proper planning has occurred, the driver will have enough 20-foot lengths of hose to connect the trailer to the tank.
Finally, it’s time to start the vacuum or blower, carefully adjusting the pressure to get the product flowing smoothly through the hose. That hose connects to a pipe that leads into the silo, sometimes by a long route that includes the occasional elbow.
Offloading usually takes about an hour to an hour-and-a-half, depending on the product. An inexperienced driver might take longer, especially if he turns the pressure up too high and must stop the operation to unclog the hose or pipes.
The tank washing station
One of the biggest differences between dry van and dry bulk trucking is the need to wash the dry bulk trailer. After dropping a load, the bulk driver might have to travel an hour or more—maybe even to another state—to find a certified tank wash station.
This requirement adds extra time to every shipment. It also adds cost, partly because every shipment includes deadhead miles, and partly because the shipper pays for the wash.
For many products, the tank wash just needs to blast the inside of the trailer with water at high pressure. It does this by dropping a spinning device—something like a disco ball with water jets all around—into each of the manholes. After the wash, the trailer is blown dry.
If the driver has just dropped a load of sand or clay and is preparing to pick up a similar load, it’s often fine to skip the certified wash and visit a local business that washes down the tank with a high-pressure hose.
But when a truck drops one commodity and picks up a different one—especially when moving plastics—it must go to a certified wash station and receive a “conversion wash.” In that process, employees at the tank wash take off the pipe that runs along the bottom of the trailer, remove all its fittings, lay everything on the ground and give it a careful cleaning.
ErectaStep access platform for a dry bulk washing station


Quick Quote 866-761-7225
LET US DESIGN YOUR SOLUTION TODAY
Our innovative tools provide 3D visualizations and accurate quotes in minutes.
Get Help NowOrder Now 866-761-7225
Questions or Need a Quote?
Chat live with a knowledgeable and friendly safety expert now.

Bob Kashtan
Located in South Carolina

Joey Robinson
Located in South Carolina

Caelin Lacy
Located in South Carolina

Katie Kelly
Located in South Carolina

Amber Graham
Located in South Carolina