Get a quote, configure a custom safety solution or ask a question. We're here to help!




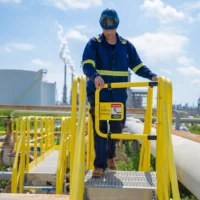



- Spill ContainmentMore …Loading Safety CagesMore …
SafeRack Worldwide
We pride ourselves on one-on-one customer service. When you call SafeRack, we'll be there to answer your questions with a combined experience of 400+ years.
Select your region below.- View Products
- Railcar & Truck Loading Platforms
- Gangways & Loading Ramps
- Stairs, Platforms & Ladders
- Mobile Ladders & Platforms
- Loading Arms & Fluid Transfer
- Safety Gates & Traffic Control
- Aviation & Aerospace Access
- Marine Access & Loading
- Grounding & Monitoring
- Spill Containment
- Loading Safety Cages
- Transloaders & Skids
- Shelters & Canopies
- Fall Protection
- Terminal & Speciality
Home / Industries / Urea Handling Design, Loading, and Installation.UREA Loading and Handling
Urea Handling Design, Loading, and Installation.
Urea is a colorless liquid with a slight ammonia odor that is produced by combining nitric acid and ammonia into a liquid solution. Farmers prefer Urea because it can be applied more uniformly than non-liquid forms of fertilizers.
In the United States, Urea is transported via rail, truck, and barge. It is typically a splash loading operation when loaded into trucks or railcars via loading arms. Urea itself does not pose an inhalation hazard. However, decomposition of Urea may produce nitrogen oxide and ammonia vapor, so operator diligence of vapors must be observed. Vapor recovery, while not required, should be considered while operators are on top of the vehicles during the loading process to further increase the level of safety during the loading/unloading process.
Urea is typically transported in 20,500 gallon tank cars. The rails cars themselves are 9′ outside diameter with an overall length of ~47′, with offset crashbox openings of varying length and widths.
Tank truck (un)loading procedures are similar to railcar applications with the trailers meeting established DOT requirements for transporting Urea or similar commodities.
Question, Get a Quote, Live Demo or Request an On-Site Visit
Our experts simplify the complex
View Full TextTypical Urea Loading Platform
Quote or discuss your installation.
Start by selecting loading application"*" indicates required fields
Below are some of the loading and unloading solutions for illustrative purposes only. Our experts will work with you and your team for a custom solution to suit your needs.
Urea Loading Arms
UREA is not a hazardous product, but it is corrosive to zinc, copper, brass, bronze, and iron. Aluminum and carbon steel are less susceptible, but stainless steel is the widely accepted material of choice for loading systems. Couple the arm with PTFE or Chemraz seals and you have a good combination of corrosion resistant materials that will hold up to the rigors of UREA loading. UREA is generally not considered an inhalation hazard. Therefore, vapor recovery is not mandated but recommended in facilities in close proximity of populated areas.
Loading Gangways and Safety Cages
A wider access gangway (36″-48″ is preferable) as it helps improve access and egress to and from the vessel. In addition, a wider gangway will reduce the risk of the operator’s PPE getting caught, torn or damaged, and will improve productivity and safety. Powered gangway solutions are also an option, with both hydraulic and pneumatic solutions being commonly used. Each gangway will be fitted with a two-rail safety cage for the railcar crash box. This will be a centered 6’x6’ safety cage to sit directly over the cashbox. This will provide a safe, secure work environment for your operator when connected to their breathing apparatus
GX SELF-ADJUSTING STAIR (SAS) GANGWAY
SafeRack’s NEW GX SAS gangways uses Retractalok power-assist technology allowing operators to raise or lower effortlessly, light as a feather to lift, solid as a rock. Tested in the most critical applications, this revolutionary new gangway outperforms all others. Available in multiple lengths and widths. Learn More
Urea Eye Wash/Drench Showers
ANSI guidelines state that an Eye Wash/Drench Showers need to be located 10 seconds or 55’ (16.8m) from contaminants or hazardous materials. Eyewash stations need to be on the same horizontal plane with no obstructions.
Therefore, we would propose the installation of a standard combination Drench Shower/Eyewash Unit, which will save limited space and fit easily into any work environment.
Urea Spill Containment
Spill containment pans will be provided at the point of loading operations and is an essential piece of equipment in overall site safety and environmental protection Urea Grounding
Urea is a flammable liquid, industry best practice includes the grounding of all vessels before starting the (un)loading process. - Vehicle grounding and bonding — ensure true grounding before product flow is permitted
- Explosion-proof enclosures — meet or exceed UL, CSA and Ex requirements
Urea Safety Gates
Safety Gates will be installed at the top of stairs and any other openings to ensure operator safety at all times. YellowGate Safety Gates
SafeRack’s line of industrial safety gates is the most flexible product on the market with the ability span openings between 16” and 36” and is field adjustable with nothing more than a wrench. Learn More
Urea Options
- Lighting – Lighting both over and under the platform will be provided. For overcast days or second shift, lighting is essential for improved safety and improved productivity.
- Platform & Canopies – Full platform canopies reduce exposure to the elements and improve the safe and productive loading operation from the operator’s perspective.
- Operator Shelter – Depending on your site requirements, consideration should be given to the requirement of an operator or guard building on the loading platform. This can be customized to meet specific site requirements
- Wheel Chocks – Railcar Wheel Chocks provide fast blocking of all types of railcars and meet OSHA regulations to safely prevent railroad cars from moving during loading or unloading operations. This is a requirement by the Department of Homeland Security
Personal Protective Equipment PPE Requirements
Eye/Face Protection: Wear chemical safety goggles. A face shield (with safety goggles) may also be necessary.
Skin Protection: Wear chemical protective clothing e.g. gloves, aprons, boots. Coveralls or long sleeve shirts and pants in some operations. Wear a chemical protective, full-body encapsulating suit, and self-contained breathing apparatus (SCBA). Suitable materials include: butyl rubber, neoprene rubber, Viton®, Viton®/butyl rubber, Barrier® – PE/PA/PE, Silver Shield® – PE/EVAL/PE, Trellchem® HPS, Trellchem® VPS, Saranex®™, Tychem® BR/LV, Tychem® Responder® CSM, Tychem® TK. The following materials should NOT be used: natural rubber, polyvinyl chloride. Recommendations are NOT valid for very thin neoprene rubber gloves (0.3 mm or less).
Respiratory Protection: Up to 5 ppm:
(APF = 10) Any chemical cartridge respirator with cartridge(s) providing protection against chlorine*; or Any supplied-air respirator*.
*Reported to cause eye irritation or damage; may require eye protection.
APF = Assigned Protection Factor
Recommendations apply only to National Institute for Occupational Safety and Health (NIOSH) approved respirators. Refer to the NIOSH pocket guide to chemical hazards for more information.
Use a local exhaust ventilation and enclosure, if necessary, to control the amount in the air. Consider using a corrosion-resistant exhaust ventilation system separate from other ventilation systems. It may be necessary to use stringent control measures such as process enclosure to prevent product release into the workplace. Use backup controls (e.g. double mechanical pump seals) to prevent the release of this material due to equipment failure. * For illustrative purposes only. Our experts will work with you and your team for a custom solution to suit your needs Urea Loading Solutions
Urea is produced in prills, granules, flakes, pellets, crystals, and solutions, but it is traditionally marketed as prills or granules. The choice of the commercial preferred form is normally associated with its application, solubility, and crushing strength.
Urea is a colorless liquid with a slight ammonia odor that is produced by combining urea, nitric acid, and ammonia into a liquid solution. Urea’s nitrogen content typically ranges from 28 to 32 percent. Farmers prefer Urea because it can be applied more uniformly than non-liquid forms of fertilizers. It can also be mixed with herbicides, pesticides, and other nutrients, enabling farmers to reduce costs by spraying once versus multiple applications. It also allows for improved safety versus anhydrous ammonia or dry ammonium nitrate. It’s easy to handle and apply accurately, plus it’s not likely to be stolen for illegal use.
Best practice loading/unloading includes: wearing chemical-resistant clothing, gloves, splash goggles to protect eyes and skin. While Urea itself does not pose an inhalation hazard, additional respiratory projection may be required to work with liquid or gaseous ammonia. Since the operators are basically regulated to wearing a restrictive chemical suit, SafeRack recommends the use of a wider gangway and an elevating safety cage for more ergonomic access and egress.
Typical Urea Loading Systems include*
Top Loading platform w/ half canopy Gangway - 36”, 48” or 60” wide galvanized or stainless-steel access gangway
- optional pneumatic raise/lower vs. manual operation
Safety Gage - 7’- 0” x 8’- 0” two rail safety fall prevention safety cage
- Optional 9’-0” W x 15’-0” L four rail elevating cage
Loading Arm(s) – 3” SST Boom Supported Loading Arm - Shut-off valve
- Parking sensor
Spill Containment Lighting Grounding System w/ Interlock Options like Operator Shelter, Windsock, Wheel Chocks… * For illustrative purposes only. Our experts will work with you and your team for a custom solution to suit your needs Urea handling
Urea is commercially produced from ammonia and carbon dioxide and takes place in two reactions. The first reaction (exothermic) of liquid ammonia with dry ice produces an intermediate product called ammonium carbamate. The second reaction (endothermic) produces urea and water.
Urea solids are produced from the urea melt by two basic methods: prilling and granulation. Prilling is a process by which solid particles are produced from molten urea that is sprayed from the top of a prill tower. As the droplets fall through a counter-current air flow, they cool and solidify into nearly spherical particles.
Granulation is a method where solids are built in layers on seed granules that are placed in a rotating drum.
Personal Protective Equipment: Face shield. Gloves. Insufficient ventilation: wear respiratory protection. Protective clothing.
Physical State: Liquid
Urea is very corrosive to most metal surfaces. When not properly managed,Urea corrosion can cause serious damage to pumps, pipelines, storage tanks, and access equipment.
Urea is not flammable. Use water to extinguish a fire involving Urea if the water is compatible with the burning material.
Suitable Extinguishing Media: Water spray.
Unsuitable Extinguishing Media: Dry chemical, carbon dioxide, or regular foam.Urea itself does not pose an inhalation hazard, however, the decomposition of Urea may produce nitrogen oxide and ammonia vapor. First aid includes immediate flushing of eyes or skin with tepid water for a minimum of 15 minutes, per ANSI guidelines. If lung irritation develops due to inhalation immediately remove the operator to fresh air and monitor. If irritation or pain persists, the operator should be taken to a health care facility.
OSHA occupational exposure limits (OEL) limits and moreTechnical Measures: Proper grounding procedures to avoid static electricity should be followed. Comply with applicable regulations.
Storage Conditions: Store in a dry, cool, and well-ventilated place. Keep container closed when not in use. Keep in a fireproof place. Keep/Store away from combustible materials, extremely high or low temperatures, direct sunlight, ignition sources, incompatible materials.
Incompatible Materials: Strong acids. Strong bases. Strong oxidizers. Halogens (F, Cl, Br, I). Chlorine compounds, chlorinated inorganics (potassium, calcium and sodium hypochlorite), and hydrogen peroxides. Organic materials. Combustible materials.
Decomposition: When the water in Urea evaporates, residue may include solid ammonium nitrate and urea. When sensitized or during decomposition, solid ammonium nitrate may become unstable and/or explosive. Urea pumps operated with blocked discharge have been known to detonate.
When Urea is heated to decomposition it may produce vapors containing nitrogen oxides (NOX) and ammonia.
Incompatibilities: Urea will form nitrogen trichloride, which may be explosive when mixed with chlorine and hypochlorites. If Urea solution has been dehydrated to ammonium nitrate and urea, refer to the incompatibility/decomposition information for those chemicals. Urea will form urea nitrate when mixed with nitric acid at low pH. Urea nitrate may become unstable and/or explosive under certain conditions.
Urea is typically loaded into open trailers via load spouts inside a silo. Access to the top of a vehicle is usually not required
Urea is produced with a two-step process where the ammonia and carbon dioxide react to form ammonium carbamate which is then dehydrated to urea. In the process, ammonia and carbon dioxide are fed to the synthesis reactor which operates at 150 bar pressure at around 180-210oC. The reaction mixture containing ammonia, ammonium carbamate, and urea is first stripped of the ammonia and the resultant solution passes through a number of decomposers operating at progressively reduced pressures. Here the unconverted carbamate is decomposed back to ammonia and carbon dioxide and recycled to the reactor.
The urea solution is concentrated by evaporation or crystallization, and the crystals can be melted to yield pure urea in the form of prills or granules. Prills are made by spraying molten urea from the top of a high tower through a counter-current air stream. Granular urea is formed by spraying molten urea into a mixture of dried urea particles and fines in a rotating drum.
Urea processes fall into two categories: external solution recycle systems, and internal solution stripping systems. In the former, energy is saved by high carbon dioxide conversion rates while the latter reduces net energy requirements by optimizing heat recovery.
Lightning Fast Urea Loading – This SafeRack loading platform, with 6” OPW top loading arms is capable of bulk loading 5,000 gallons of urea ammonium nitrate in under 4 minutes. Located at a Northern California fertilizer facility, this 2-spot loading platform increases throughput without sacrificing safety. Installation includes two SafeRack gangways, safety cages, and OPW top loading arms. Custom Tracking Gangway With Extension Wings Custom Metal Tracking Gangway Installation Chlorine 101
Things to know about UREA
Urea is not listed as a hazardous material per DOT shipping regulations.
Urea, also known as carbamide is a processed form of ammonia used as a feed ingredient and crop nutrient, with the chemical formula CH4N2O. It has the highest nitrogen content of all solid fertilizers at 46% N. UAN solutions such as 28% and 32% liquid nitrogen, are made up of different forms of nitrogen. Example: 28% liquid nitrogen is 50% Urea, 25% ammonium and 25% nitrate.
The primary function of Urea fertilizer is to provide plants with nitrogen to promote green leafy growth and it also aids in the photosynthesis process of plants. It is highly soluble in water and non-toxic.
Urea is a colorless liquid with a slight ammonia odor. It is a solution of ammonium nitrate in water that is used as a fertilizer. It can also be mixed with herbicides, pesticides, and other nutrients, enabling farmers to reduce costs by spraying once versus multiple applications. It also allows for improved safety versus anhydrous ammonia or dry ammonium nitrate and is not likely to be stolen for illegal use.
Urea is stable under normal storage and handling and is non-flammable; however, it may form an explosive salt in the presence of nitric acid. Urea also reacts violently with gallium perchlorate.
Customer Reviews
5 5Your competition is not really comparable.SafeRack has the sales staff to support your product and it was easy and efficient to obtain information to help me secure a sale. Product was delivered on time as promised. All shipping information was given to prepare for pick up and delivery efficiently. I hope to work with SafeRack more closely to secure more business here in Quebec. Your competition is not really comparable, pricing may be lower but the quality is nothing like yours. I do not work with any other suppliers in this field. SafeRack is the only product we promote to our customers when the need is there.
By Nadia Boismenu from Hi Tech Piping on 5/6/145 5Very satisfied with the service we get from the equipment.We have purchased them numerous times and are very satisfied with the service we get from the equipment.
By Steve Taylor from Cemex on 5/5/165 5Extremely Satisfied with the fall protection harnessReliable service, good communication.
By Joe Burkhardt from All Mine Paving on 5/17/215 5Service, quality and ease of use…Very fast delivery. Very good quality and service from salesman and everyone else.
By Dua Thor from Sanimax ATO Inc. on 6/6/174 5Overall I’m satisfied.Custom application. Customer service, from salesperson Molly Laqua, has been very responsive. Delivery was as requested and on time. Overall I’m satisfied to date. Three benefits about this SafeRack product: SafeRack installation ability, professional field crews, and responsive sales team.
By John Conner from Momentive Specialty Chemicals Inc. on 1/15/135 5Fit is very good and simple to operate.The dry lock valve is well made – fit is very good and simple to operate.
By Phillip Wendel from Archer Daniel Midland on 3/3/11Is your plant or facility compliant with ANSI, OSHA, and local safety codes? We can help!
EMERGENCY EYEWASHES / SHOWER EQUIPMENT AND THE ANSI/ISEA Z358.1 – 2014 STANDARD
Following eye contact, you must start washing with water immediately to prevent permanent damage. In the event of skin contact, you must start washing with water immediately to prevent slow-healing chemical burns.
Are you aware that ANSI guidelines state that Eye Wash/Drench Showers need to be located 10 seconds or 55′ from contaminates or hazardous materials and located on the same horizontal plane, with no obstructions? If bottom loading/unloading, an additional shower should be located at grade as well. SafeRack provides the above equipment plus much more needed to keep employees safe and expedite bulk chemical loading and unloading.
OSHA Regulation Experts – Does your existing chemical safety equipment or chemical loading systems meet OSHA’s latest requirements? SafeRack’s professional technical sales consultants are available to meet with your team to make recommendations to keep your facility in front of OSHA’s ever-changing country and region-specific standards and regulations, including lifeline and trolley beam fall arrest systems, metal stairs, and access platforms.
Installation Gallery
Why SafeRack?
The SafeRack approach is a collaborative one. Let’s call it The SafeRack Way. We have, over many years amassed a great deal of experience and understanding of the safety aspects involved in loading road tankers and railcars, as well as the behavioral habits of the operators.
Experts In Chemical Loading
- Acetic Acid
- Acetic Anhydride
- Acetonitrile
- Acrolein
- Acrylic Acid
- Acrylonitrile
- Aluminum Chloride
- Aluminum Sulfate
- Ammonia
- Ammonium Hydroxide
- Ammonium Nitrate
- Aniline
- Benzene
- Benzyl Chloride
- Bromotrifluoromethane
- Butadiene
- Carbon Dioxide
- Caustic
- Chlorine
- Chloroform
- Chlorosulfonic Acid
- DEF (Diesel Exhaust Fluid)
- Diethylene Glycol
- Dimethylformamide
- Dodecylbenzene Sulfonic Acid
- Ethanol
- Ethyl Acetate
- Ethyl Chloride
- Ethylene
- Ethylene Dichloride
- Ethylene Glycol
- Ethylene Oxide
- Ferric Chloride
- Ferrous Chloride
- Hexane
- Hydrochloric Acid
- Hydrofluoric Acid
- Hydrofluorosilicic Acid
- Hydrogen Cyanide
- Hydrogen Peroxide
- Hydrofluoric Acid
- Hypochlorous Acid
- Isopropyl Acetate
- Liquid Argon
- Liquid Nitrogen
- Liquid Oxygen
- Maleic Anhydride
- MDI
- Methanol
- Methyl Chloride
- Methyl Ethyl Ketone
- Methyl Methacrylate
- Methyl Isocyanate
- Molten Sulphur
- Nitric Acid
- Oleum
- Phenol
- Phosphoric Acid
- Phosphorus Oxychloride
- Phosphorus Trichloride
- Polypropylene
- Renewable Diesel
- Sodium Cyanide
- Sodium Hydroxide
- Sodium Hypochlorite
- Styrene Monomer
- Sulfuric Acid
- Sulfur Dioxide
- Titanium Tetrachloride
- Toluene
- Toluene Diisocyanate
- Turpenitne
- UAN (Urea Ammonium Nitrate)
- UREA
- Vinyl Acetate
- Vinyl Chloride
- Xylene
- Zinc Chloride
- Agro-Chemical
- Specialty Chemical
- Petrochemical
North America’s largest loading terminal
World-leading designer, manufacturer, and installer of truck and railcar loading platforms
As one of the primary railcar loading points, Hardisty is one of the major crude oil hubs in North America and a major origination point of pipelines that export to the United States. SCS was asked to supply and construct a SafeRack crude oil loadout terminal spanning nearly half a mile. The USD Hardisty terminal can load up to two 120-railcar unit trains per day and consists of a fixed loading rack with 62 railcar loading positions enclosed, separate control, operator, and mechanical buildings, as well as a unit train staging area and loop tracks capable of holding multiple unit trains simultaneously. SCS also supplied and installed boom-supported loading arms with supply and vapor management systems.


Quick Quote 866-761-7225
LET US DESIGN YOUR SOLUTION TODAY
Our innovative tools provide 3D visualizations and accurate quotes in minutes.
Get Help NowOrder Now 866-761-7225
Questions or Need a Quote?
Chat live with a knowledgeable and friendly safety expert now.

Bob Kashtan
Located in South Carolina

Joey Robinson
Located in South Carolina

Caelin Lacy
Located in South Carolina

Katie Kelly
Located in South Carolina

Amber Graham
Located in South Carolina