Get a quote, configure a custom safety solution or ask a question. We're here to help!




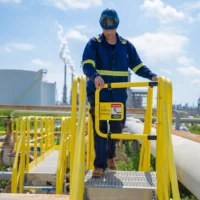



- Spill ContainmentMore …Loading Safety CagesMore …
SafeRack Worldwide
We pride ourselves on one-on-one customer service. When you call SafeRack, we'll be there to answer your questions with a combined experience of 400+ years.
Select your region below.- View Products
- Railcar & Truck Loading Platforms
- Gangways & Loading Ramps
- Stairs, Platforms & Ladders
- Mobile Ladders & Platforms
- Loading Arms & Fluid Transfer
- Safety Gates & Traffic Control
- Aviation & Aerospace Access
- Marine Access & Loading
- Grounding & Monitoring
- Spill Containment
- Loading Safety Cages
- Transloaders & Skids
- Shelters & Canopies
- Fall Protection
- Terminal & Speciality
Home / Industries / Bulk Chemical Loading / Butadiene Handling Design, Loading, and Installation.Butadiene (C4H6) Handling Design, Loading, and Installation.
What is Butadiene? As an Olefin in the Petrochemical family tree, Butadiene is a chemical made from the processing of petroleum. It’s primarily used as a monomer to manufacture many different types of polymers and copolymers, and as a chemical intermediate in the production of industrial chemicals, including synthetic rubber. Synthetic rubber is widely used for tires on cars and trucks. Butadiene is also used to make plastics, including acrylics, and small amounts are found in gasoline. Butadiene is the 36th highest volume chemical produced in the United States.
In the United States, Butadiene is a “tight-fill” (closed-loop) loading operation and is loaded into road tankers and rail cars via chemical hoses or top loading arms with vapor recovery. Butadiene, if not handled properly can be fatal and Personal Protective Equipment (PPE) is required. Additionally, because operators are on top of the vehicles during the loading process, fall prevention is essential, not only for safety but increases throughput.
Question, Get a Quote, Live Demo or Request an On-Site Visit
Our experts simplify the complex
View Full TextYour Project
Typically, as a starting point, we will need to know answers to these questions for your project
- The Railcar connection locations need flexibility – Do you know what the breadbasket connections look like?
- Are you using liquid and vapor arms/hose as two separate devices or a piggyback arm?
- Is the loading station indoors or outdoors?
- Is the loading area temperature controlled?
- How are you going to spot your railcars
Our highly trained technical sales team will undertake a detailed site survey prior to undertaking any work to check and clarify all dimensions, obstructions, access issues and other salient points. Our challenge is to provide the safest working environment – protecting operators and the equipment – while simultaneously enabling you to improve throughput and productivity.
Your Project Needs
Whether you are looking for a turn-key installation, on-site supervision or a maintenance program, SafeRack is positioned to assist you. We can do as little or as much as you need. Our project management and supervision team is the best in the business at supporting your company’s needs.
- Collaborative Design – Our loading platform specialists will work with you one on one, if you design to design the best loading solution for your specific needs
- Contract review – drawings and associated documents relating to the contract prior to site arrival
- Risk Assessment – Undertaking a site risk assessment
- Shipment Inspection – Detection of any shipping damage or abnormalities
- Material Receiving – Supervised off-loading and transport at site
- Installation Management – Supervised Installations and Coordination
- Start-up & Commissioning – On-site training for both users and maintenance personnel
Loading Arms
Generally speaking, SafeRack recommends rigid pipe loading arms where possible for the following reasons:
- Balanced throughout their movement envelope
- Designed not to hit the ground – protecting the asset and the operator
- Ergonomic – one man operation
- Fitted with manual or actuated valves.
- Fitted with optional purge/vent facilities
- Can be moved into position with ease and left hanging in the air while the operator prepares the tanker connection
- Parked neatly
Hoses require:
- Annual pressure test
- Are difficult to stow neatly when not in use
- Can be dropped
- Can be driven over
- Are very heavy to use if fitted with a valve at the tanker connection point
- Cannot be easily heated or have vent/purge valves fitted to it
- Prone to catastrophic failure
Butadiene is typically transported via DOT-106 unpressurized general service tank cars.
However, the railcars are designed for pressure relief in order to accommodate thermal expansion during transit, similar to transporting ethanol, gasoline, jet fuel, and other distillates.
The rails cars themselves are 9′ outside diameter with an overall length of ~47′, with a 6’ x 6′ or 8’ x 8’ centered crash box.
Tank truck (un)loading procedures are similar to railcar applications with the trailers meeting established DOT requirements for hauling methanol or like commodities. Approved DOT trailers include MC 300 thru MC 312, MC 330, and MC 331. All trailers must be equipped with pressure relief valves; and trailers with bottom outlets must be equipped with remote-controlled stop valves. Air pressurization of the tanks (air padding) must never be used for methanol unloading.
Typical Butadiene Loading Platform
Quote or discuss your installation.
Start by selecting loading application"*" indicates required fields
Below are some of the loading and unloading solutions for illustrative purposes only. Our experts will work with you and your team for a custom solution to suit your needs.
Butadiene Top Loading Arms
Butadiene is typically loaded into railcars via chemical hoses or loading arms. The current best loading practice is to use a 3″ chemical hose or a carbon steel loading arm with quick-acting coupling, often in the form of Hammer Unions with stabber pipe. The chemical hose or loading arm will have a top inlet with a control valve to ensure that it is self-draining after use and is supported along the length of a mechanical loading arm to improve handling; this is known as a by-pass arm. You can install one liquid and one vapor arm, or mount both the liquid and vapor hoses on one by-pass arm. The alternative is to have a supported boom top loading arm, top inlet, with vapour cone, and vapour return hose. The arm would be fitted with an overfill device and the vapour hose can be fitted with an over-pressurization sensor.
Break-away couplings can be fitted near the inlet of the hose for additional safety in the event of a premature departure.
Butadiene Un-Loading Arms
Typically, the butadiene will be gravity unloaded via a rigid carbon steel self-draining unloading arm. Breathing vents are opened on the vessel to allow the product to drain. This can also be achieved through the use of hoses and couplings.
Butadiene bottom loading valves on tank railcar Marine Access Gangway
Butadiene is typically pumped from dockside side storage tanks into sealed cargo holds of double hull barges. To facilitate safe, secure access and egress from the barges, SafeRack offers a complete line of marine gangways. SafeRack’s GX SAS gangways use Retractalok power-assist technology allowing operators to raise or lower effortlessly, light as a feather to lift, and solid as a rock. Tested in the most critical applications, this revolutionary new gangway outperforms all others. Available in multiple lengths and widths.
Learn MoreMAXRack Elevating Safety Cage
As an alternative to our two and four-rail safety cages, some customers prefer our MAXRack elevating safety cages. The ultimate fall prevention solution engineered to keep operators safe and productive. Designed for both trucks or railcars, and available in multiple cage lengths and widths. Safe, durable, and easy to use. MAXRack is built rock-solid with galvanized steel column supports and lifting arms (cages can be Aluminum, Galvanized, or Stainless Steel depending on application) Available in two power options – Pneumatic Air Drive and Electric Drive (Explosion and Non-Explosion Proof).
Learn MoreButadiene Top Loading Arms
Butadiene is typically loaded into railcars via chemical hoses or loading arms. The current best loading practice is to use a 3″ chemical hose or a carbon steel loading arm with quick-acting coupling, often in the form of Hammer Unions with stabber pipe. The chemical hose or loading arm will have a top inlet with a control valve to ensure that it is self-draining after use and is supported along the length of a mechanical loading arm to improve handling; this is known as a by-pass arm. You can install one liquid and one vapor arm, or mount both the liquid and vapor hoses on one by-pass arm. The alternative is to have a supported boom top loading arm, top inlet, with vapour cone, and vapour return hose. The arm would be fitted with an overfill device and the vapour hose can be fitted with an over-pressurization sensor.
Break-away couplings can be fitted near the inlet of the hose for additional safety in the event of a premature departure.
Butadiene Eye Wash/Drench Showers
ANSI guidelines state that an Eye Wash/Drench Showers need to be located 10 seconds or 55’ (16.8m) from contaminants or hazardous materials. Eyewash stations need to be on the same horizontal plane with no obstructions.
Therefore, we would propose the installation of a standard combination Drench Shower/Eyewash Unit, which will save limited space and fit easily into any work environment.
Butadiene Spill Containment
Spill containment pans will be provided at the point of loading operations and is an essential piece of equipment in overall site safety and environmental protection. Butadiene Grounding
While not highly flammable, high airborne concentrations can be ignited and pose a significant fire and explosion hazard, especially in confined spaces. Steel containers or vessels of ammonia may also explode when subject to excessive heat or high temperatures. Industry best practice includes the grounding of all vessels prior to starting the (un)loading process. - Vehicle grounding and bonding — ensure true grounding before product flow is permitted
- Explosion-proof enclosures — meet or exceed UL, CSA, and Ex requirements
Safety Gates Butadiene Loading Applications
Safety Gates will be installed at the top of stairs and any other openings to ensure operator safety at all times. YellowGate Safety Gates
SafeRack’s line of industrial safety gates is the most flexible product on the market with the ability span openings between 16” and 36” and is field adjustable with nothing more than a wrench. Learn More
Butadiene Loading Platform Options
- Lighting – Lighting both over and under the platform will be provided. For overcast days or second shift, lighting is essential for improved safety and improved productivity.
- Platform & Canopies – Full platform canopies reduce exposure to the elements and improve the safe and productive loading operation from the operator’s perspective.
- Operator Shelter – Depending on your site requirements, consideration should be given to the requirement of an operator or guard building on the loading platform. This can be customized to meet specific site requirements
- Wheel Chocks – Railcar Wheel Chocks provide fast blocking of all types of railcars and meet OSHA regulations to safely prevent railroad cars from moving during loading or unloading operations. This is a requirement by the Department of Homeland Security
Personal Protective Equipment PPE Requirements
Eye/Face Protection: Wear chemical safety goggles. A face shield (with safety goggles) may also be necessary.
Skin Protection: Wear chemical protective clothing e.g. gloves, aprons, boots. Coveralls or long sleeve shirts and pants in some operations. Wear a chemical protective, full-body encapsulating suit, and self-contained breathing apparatus (SCBA). Suitable materials include: butyl rubber, neoprene rubber, Viton®, Viton®/butyl rubber, Barrier® – PE/PA/PE, Silver Shield® – PE/EVAL/PE, Trellchem® HPS, Trellchem® VPS, Saranex®™, Tychem® BR/LV, Tychem® Responder® CSM, Tychem® TK. The following materials should NOT be used: natural rubber, polyvinyl chloride. Recommendations are NOT valid for very thin neoprene rubber gloves (0.3 mm or less).
Respiratory Protection: Up to 5 ppm:
(APF = 10) Any chemical cartridge respirator with cartridge(s) providing protection against Butadiene*; or Any supplied-air respirator*.
*Reported to cause eye irritation or damage; may require eye protection.
APF = Assigned Protection Factor
Recommendations apply only to National Institute for Occupational Safety and Health (NIOSH) approved respirators. Refer to the NIOSH pocket guide to chemical hazards for more information.
Use a local exhaust ventilation and enclosure, if necessary, to control the amount in the air. Consider using a corrosion-resistant exhaust ventilation system separate from other ventilation systems. It may be necessary to use stringent control measures such as process enclosure to prevent product release into the workplace. Use backup controls (e.g. double mechanical pump seals) to prevent the release of this material due to equipment failure. * For illustrative purposes only. Our experts will work with you and your team for a custom solution to suit your needs Butadiene (C4H6) – Product Overview:
Butadiene is regulated by the U.S. Department of Transportation (DOT) and is classified as a hazardous and flammable material, with the DOT identification number UN 1010.
Butadiene is a colorless gas that is practically insoluble in water but very soluble in acetone, benzene, and ethanol. It is shipped as a liquefied gas under its vapor pressure, Contact with liquid can cause frostbite. When heated, butadiene emits acrid fumes, is flammable, and easily ignitable. In the presence of air, it oxidizes to form explosive peroxides and can asphyxiate an operator by the displacement of air. Its vapors are heavier than air and a flame can flashback to the source of leak very easily.
In the event of a spill or leak, immediately put on an escape-type respirator and exit the area. Eliminate heat and ignition sources such as sparks, open flames, hot surfaces, and static discharge. Post “No Smoking” signs.
Butadiene is irritating to the eyes, skin, and respiratory tract. Long term exposure has been linked to leukemia, tumors, and cardiovascular diseases.
OSHA Permissible Exposure Limit (PEL) @ 10 parts per million.
Petrochemicals are made from either petroleum or natural gas feedstock. A wide variety of petrochemicals are created/produced depending on the process.
- Aromatics – Aromatics are hydrocarbons that consist exclusively of the elements carbon and hydrogen. Common Aromatics are Benzene, Toluene, and Xylenes. Often used for creating Dyes, synthetic detergents, fibers, and plastics.The catalytic reforming of naphtha produces aromatics, which include benzene, toluene, and xylene. Together they are referred to as BTX and are predominantly obtained from petroleum refineries by the extraction from the reformate produced in catalytic reformers using naphtha obtained from petroleum refineries.
- Olefins – The most reactive class of hydrocarbons tend to crack. Common Olefins are Ethylene, Propylene, and Butadiene. Often used for creating plastics, and synthetic rubber. Chemical plants produce olefins by steam cracking of natural gas liquids like ethane and propane. Olefins include ethene, propene, and butadiene. Ethylene and propylene are chief sources of both plastic products and industrial chemicals. Butadiene is mainly used in the production of synthetic rubber.
- Synthesis gas (SynGas) – A mixture comprising of carbon monoxide, carbon dioxide, and hydrogen. Common Synthesis Gas is Ammonia and Methanol. Often used for creating Fertilizers and explosives. Synthesis gas is a mixture of carbon monoxide and hydrogen used to make ammonia and methanol. Ammonia is used to make the fertilizer urea, and methanol is used as a solvent and chemical intermediate. Steam crackers are not to be confused with steam reforming plants used to produce hydrogen and ammonia.
Customer Reviews
5 5You can not put a cost on quality.Your product wasn’t the cheapest, but the quality, design, customer service and speed of delivery proves you can not always put a cost on quality and product.
By Ed Woodall from Florida Rock & Tank Lines, Inc. on 5/31/125 5The product was delivered within the week.My salesperson was always responsive, within 24hrs of reaching out. The YellowGate is exactly what we were looking for.
By JR Dunz from Healing Place Church on 11/15/164 5Delivered in a timely fashion.Product was delivered on the date that we were told it would be delivered, in a timely fashion. The product met our needs, and was of good quality. Our sales person was courteous and kept us well informed as to when the product would be delivered.
By Bill Mason from Marysville Gas Liquids on 9/19/135 5Exceptionally fast!Great quality and service… and level of safety.
By Romis Reyes from Ash Grove Cement on 3/7/185 5Extremely SatisfiedGreat service on the phone. Very accommodating.Thank youBy Jill Luciano from Lansirlart Studios LLC on 5/4/224 5SafeRack products are well built, safe, and reliable.Our sales rep, Charles MacEachern, was professional, courteous and very helpful. I like SafeRack products because they’re well built, safe and reliable. Not to mention you have a great customer support department. Everything is positive, no negativity on any dealings with your company.
By Ralph Sprenger from LDM Yorkton Processing GP on 8/7/12Is your plant or facility compliant with ANSI, OSHA, and local safety codes? We can help!
EMERGENCY EYEWASHES / SHOWER EQUIPMENT AND THE ANSI/ISEA Z358.1 – 2014 STANDARD
Following eye contact, you must start washing with water immediately to prevent permanent damage. In the event of skin contact, you must start washing with water immediately to prevent slow-healing chemical burns.
Are you aware that ANSI guidelines state that Eye Wash/Drench Showers need to be located 10 seconds or 55′ from contaminates or hazardous materials and located on the same horizontal plane, with no obstructions? If bottom loading/unloading, an additional shower should be located at grade as well. SafeRack provides the above equipment plus much more needed to keep employees safe and expedite bulk chemical loading and unloading.
OSHA Regulation Experts – Does your existing chemical safety equipment or chemical loading systems meet OSHA’s latest requirements? SafeRack’s professional technical sales consultants are available to meet with your team to make recommendations to keep your facility in front of OSHA’s ever-changing country and region-specific standards and regulations, including lifeline and trolley beam fall arrest systems, metal stairs, and access platforms.
Why SafeRack?
The SafeRack approach is a collaborative one. Let’s call it The SafeRack Way. We have, over many years amassed a great deal of experience and understanding of the safety aspects involved in loading road tankers and railcars, as well as the behavioral habits of the operators.
Experts In Chemical Loading
- Acetic Acid
- Acetic Anhydride
- Acetonitrile
- Acrolein
- Acrylic Acid
- Acrylonitrile
- Aluminum Chloride
- Aluminum Sulfate
- Ammonia
- Ammonium Hydroxide
- Ammonium Nitrate
- Aniline
- Benzene
- Benzyl Chloride
- Bromotrifluoromethane
- Butadiene
- Carbon Dioxide
- Caustic
- Chlorine
- Chloroform
- Chlorosulfonic Acid
- DEF (Diesel Exhaust Fluid)
- Diethylene Glycol
- Dimethylformamide
- Dodecylbenzene Sulfonic Acid
- Ethanol
- Ethyl Acetate
- Ethyl Chloride
- Ethylene
- Ethylene Dichloride
- Ethylene Glycol
- Ethylene Oxide
- Ferric Chloride
- Ferrous Chloride
- Hexane
- Hydrochloric Acid
- Hydrofluoric Acid
- Hydrofluorosilicic Acid
- Hydrogen Cyanide
- Hydrogen Peroxide
- Hydrofluoric Acid
- Hypochlorous Acid
- Isopropyl Acetate
- Liquid Argon
- Liquid Nitrogen
- Liquid Oxygen
- Maleic Anhydride
- MDI
- Methanol
- Methyl Chloride
- Methyl Ethyl Ketone
- Methyl Methacrylate
- Methyl Isocyanate
- Molten Sulphur
- Nitric Acid
- Oleum
- Phenol
- Phosphoric Acid
- Phosphorus Oxychloride
- Phosphorus Trichloride
- Polypropylene
- Renewable Diesel
- Sodium Cyanide
- Sodium Hydroxide
- Sodium Hypochlorite
- Styrene Monomer
- Sulfuric Acid
- Sulfur Dioxide
- Titanium Tetrachloride
- Toluene
- Toluene Diisocyanate
- Turpenitne
- UAN (Urea Ammonium Nitrate)
- UREA
- Vinyl Acetate
- Vinyl Chloride
- Xylene
- Zinc Chloride
- Agro-Chemical
- Specialty Chemical
- Petrochemical
North America’s largest loading terminal
World-leading designer, manufacturer, and installer of truck and railcar loading platforms
As one of the primary railcar loading points, Hardisty is one of the major crude oil hubs in North America and a major origination point of pipelines that export to the United States. SCS was asked to supply and construct a SafeRack crude oil loadout terminal spanning nearly half a mile. The USD Hardisty terminal can load up to two 120-railcar unit trains per day and consists of a fixed loading rack with 62 railcar loading positions enclosed, separate control, operator, and mechanical buildings, as well as a unit train staging area and loop tracks capable of holding multiple unit trains simultaneously. SCS also supplied and installed boom-supported loading arms with supply and vapor management systems.


Quick Quote 866-761-7225
LET US DESIGN YOUR SOLUTION TODAY
Our innovative tools provide 3D visualizations and accurate quotes in minutes.
Get Help NowOrder Now 866-761-7225
Questions or Need a Quote?
Chat live with a knowledgeable and friendly safety expert now.

Bob Kashtan
Located in South Carolina

Joey Robinson
Located in South Carolina

Caelin Lacy
Located in South Carolina

Katie Kelly
Located in South Carolina

Amber Graham
Located in South Carolina